When the pressure to finish a job starts to ratchet up, things can get pretty tense in the trailer. There are a lot of irons in the fire, and a lot of opinions as to how to best get the job done. When tempers flair on your projects, what can you do to help resolve conflict and get everybody back to work?
We’ve put together 6 steps you can start using today to resolve future conflicts on your jobsites.
Continue reading “Stop the Fighting!”
The IGLC 2016 Conference has the Touchplan crew thinking about Lean Construction and Lean Project Management. We’ve been so focused on talking to you about our smarter planning initiatives that we haven’t discussed Lean in a while. Here is a quick tutorial to explain the whole Lean thing, if you are curious.
Continue reading “What is Lean Project Management?”
The weekly work meeting is your weekly check-in to make sure that everyone is on track to complete their upcoming scheduled work. It is an opportunity for everyone to hear from all team members and obtain their commitments for completing next week’s work. A successful meeting will result in a smooth and steady work flow. Only tasks without any known constraints are included in the Weekly Work Plan. The goal is to explore the links between tasks and prevent team members from overcommitting. Here are some common mistakes to avoid.
Continue reading “Weekly Work Meetings – 4 Common Mistakes”
According to the World Economic Forum’s publication Shaping the Future of Construction–A Breakthrough in Mindset and Technology there is a great need for greater productivity in construction. The last half century saw other business sectors experience surges in productivity, while the advances in construction have been meager at best.
Continue reading “Skanska discovers shipwreck in Boston Seaport District”
According to the World Economic Forum’s publication Shaping the Future of Construction–A Breakthrough in Mindset and Technology there is a great need for greater productivity in construction. The last half century saw other business sectors experience surges in productivity, while the advances in construction have been meager at best.
Continue reading “Productivity Boosts Needed in Construction”
If you already understand the broad terms of what Lean is, then we can get into specifics and look at the six guiding principles of Lean. Remember that the goal of the system is to increase efficiency by reducing waste. We accomplish our money saving goals by improving the means to our ends. These principles outline the necessary steps for creating the right means to create the right end result. They serve as a step-by-step path to most efficiently implement Lean principles in your business. And you want to implement Lean principles because they save you money.
Continue reading “Lean Principles”
The Last Planner® System, or Last Planner®, is a short-term production planning system designed to produce predictable workflow and rapid learning in programming, designing, commissioning, and construction of projects. The name refers to the person on site who can ensure predictable workflow downstream. Owners, clients or construction companies can use Last Planner® to achieve better performance in design and construction through increased schedule and program predictability.
Last Planner® was developed by Glenn Ballard and Greg Howell.
The five steps of Last Planner® are:
Master Scheduling
To start, identify your high-level project milestones for significant phases of your project, typically six months out. Examples of these milestones would be steel structure topped off, building weathertight, rough-ins complete, site finishes complete, etc.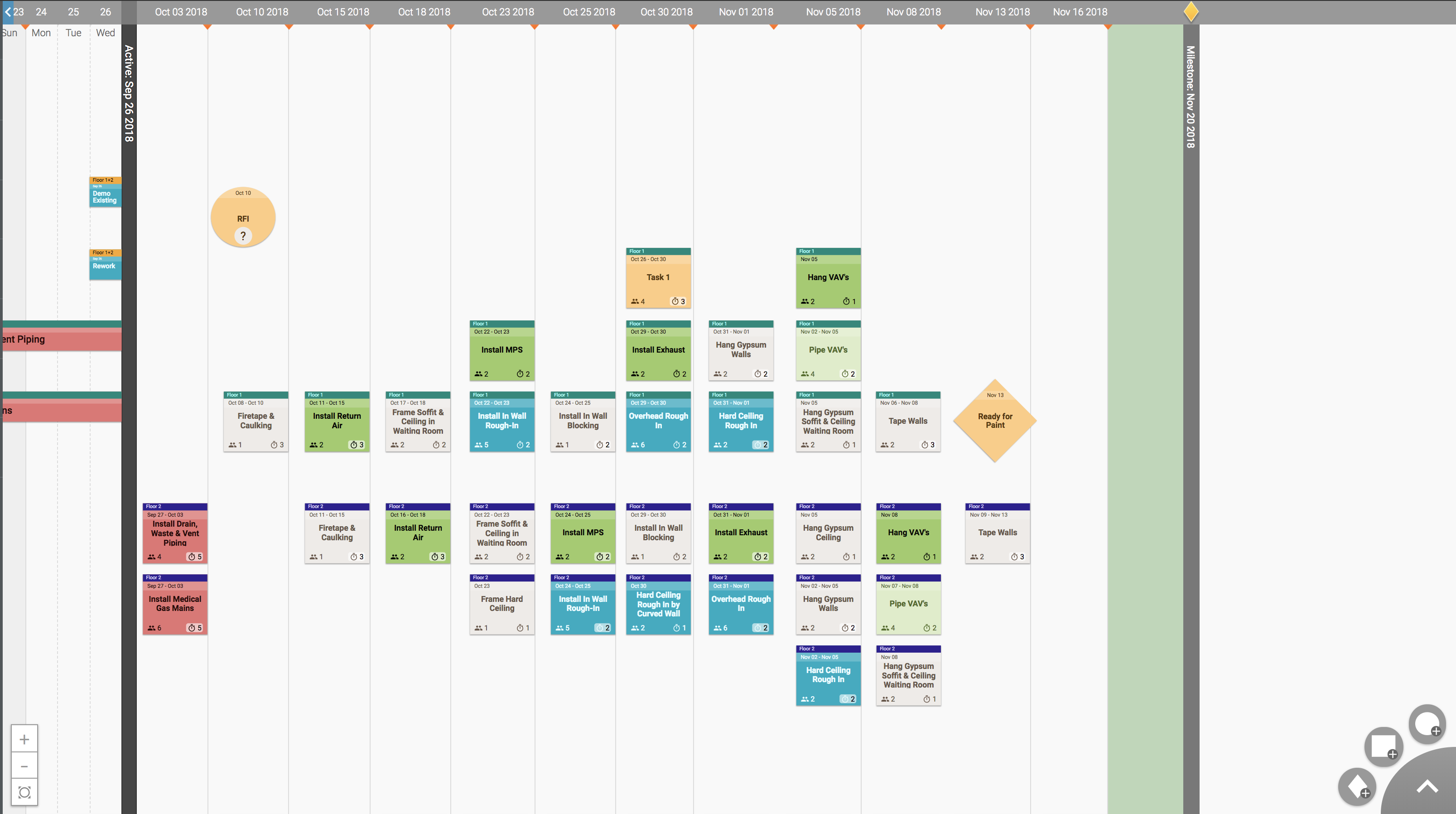
Phase Scheduling
Engage the last planners (foremen and PMs) in pull planning sessions to collaboratively establish the flow of work for the project milestones. Specify handoffs between trades within each phase schedule to ensure smooth and reliable workflow for the next six to eight weeks of work.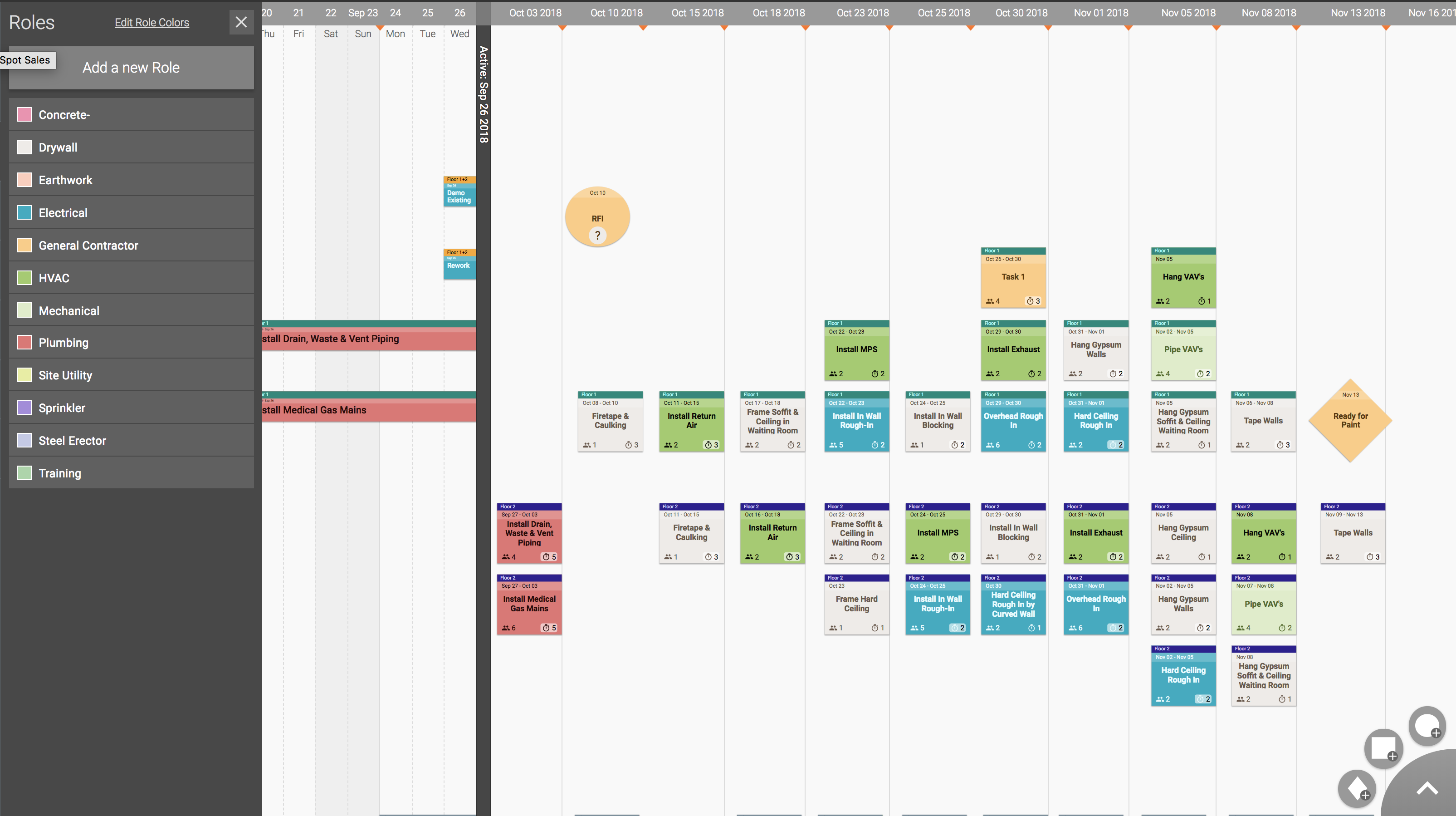
Make Work Ready Planning
This involves looking out several weeks and identifying any constraints that would keep work from starting as scheduled. Review your plan for the upcoming four to six weeks and work collaboratively to make work ready by removing constraints. Promise work for execution in a productive and effective manner and replan as necessary.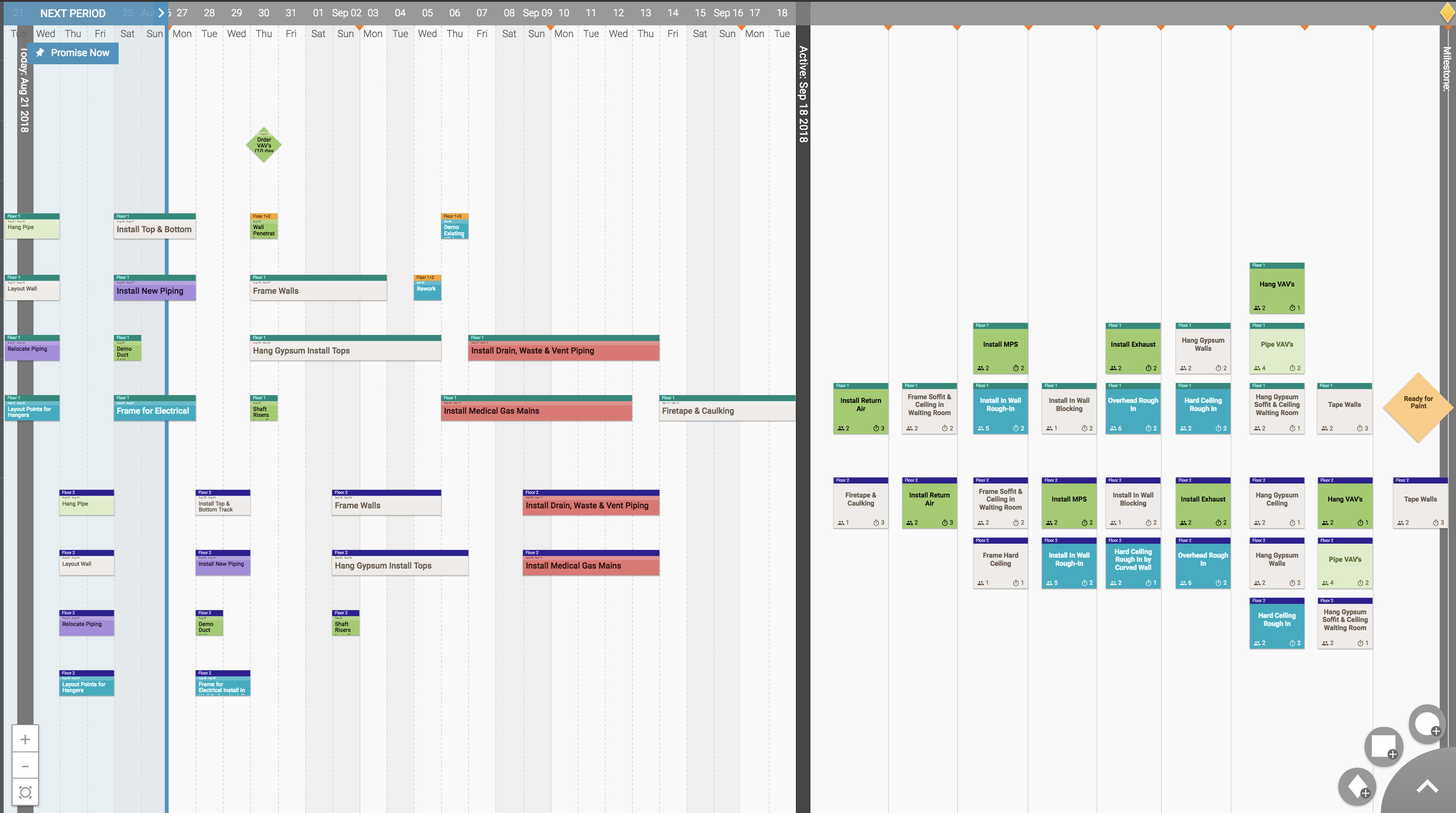
Weekly Work Planning
Talk through the upcoming week and make commitments to perform work in a certain sequence. Planners should only promise work that is unconstrained and start work that is ready. Engage the last planners in planning their work from the phase plan through daily coordination.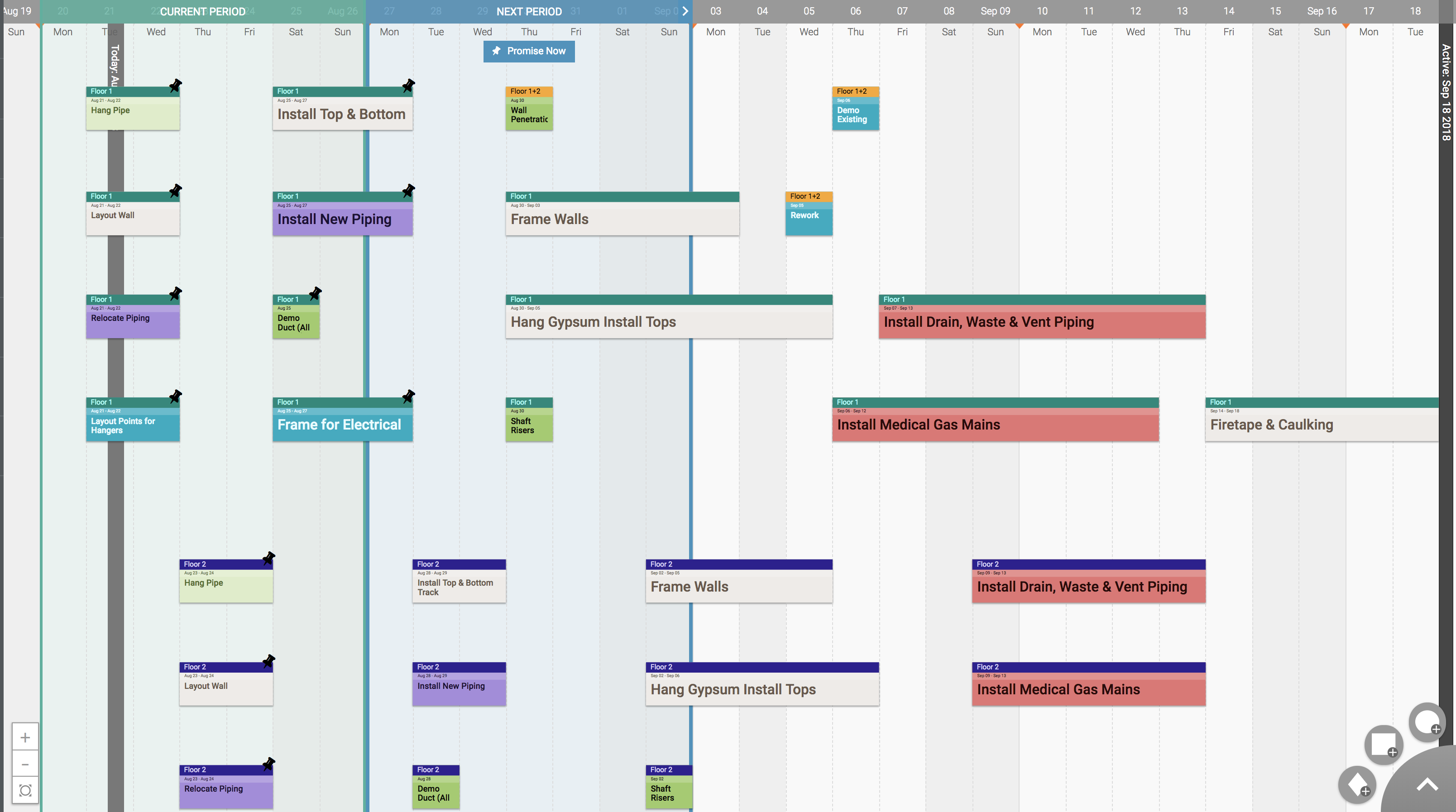
Learning
Evaluate the successes and failures of the previous week’s plan. Review the percent plan complete (PPC) and variance categories. Identify root causes of plan failures and develop a plan for implementing lessons learned.%20LPS%205%20Steps-1.png)
The Last Planner® System is a realistic way to collaboratively manage project-based production. It enables issues to be identified and resolved and increases the chances that workflows and projects are completed on time.
Lean is a means to save your company money. It is a strategy by which we avoid making tradeoffs in time, cost, and quality. But don’t just take our word for it. Here are examples of real life projects completed under budget.
Project |
Budgeted |
Actual Cost |
% Saved |
Seattle Children’s Hospital |
$110,000,000 |
$79,000,000 |
28 |
Orlando Chilled Water Plant |
$6,000,000 |
$5,400,000 |
10 |
Toronto Office TI |
$11,250,000 |
$10,530,000 |
6.4 |
In addition to projects completed under budget, it is also possible to compare similar projects with different design systems. The projects below occurred at the same time, in the same city, with the same architect. The only difference is that the contractors used different delivery models.
These are the end results for two hospitals contracted by Universal Health Services.
|
Traditional Build |
Lean Build |
Beds |
54 |
60 |
Bid Amount |
$8,828,677 |
$8,206,072 |
Change Requests |
30 |
3 |
Change Order Costs |
$677,758 |
-$36,181 |
Final Cost |
$9,500,000 |
$8,169,891 |
Lean is the means to save your company money. Lots of money. When starting the basic research into Lean, this fact gets lost in between the explanations of capturing value, pull planning and the Toyota Way. At its core, Lean is the means to save money through a reduction of waste and an increase of efficiency. It is the strategy by which we avoid making tradeoffs in time, cost, and quality.
Continue reading “What Is Lean? A Beginner’s Guide.”
We know that constraints are those directives, resources and prerequisite work needed to start and complete a task. Constraints can fall through the cracks if you don’t stay on top of checking the constraint log regularly.
Continue reading “Technology and Constraint Logs”