Lean Construction Planning Software
Transform Your Lean Construction Planning with Touchplan: From Sticky Notes to Digital Collaboration and Real-Time, Data-Driven Insights
Touchplan and Lean Construction Planning
Touchplan supports each phase of the Last Planner System® (LPS) by providing a platform for detailed visualization, collaborative planning, real-time updates, and data-driven insights. Here’s how Touchplan supports each phase:

Learn How We Make Lean Construction Planning Easy
- Simplify pull planning
- Access insights into PPC, ticket statuses, milestones, constraints, team activity, crew planning, and more
- Track commitments
- Generate reports instantly
- Manage crews and visualize staffing plans
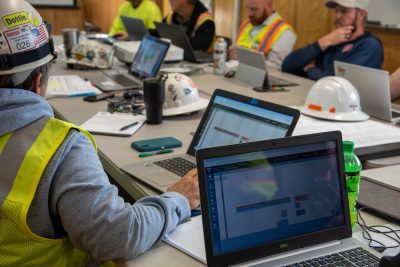
Touchplan's Lean Construction Clients See the Benefit
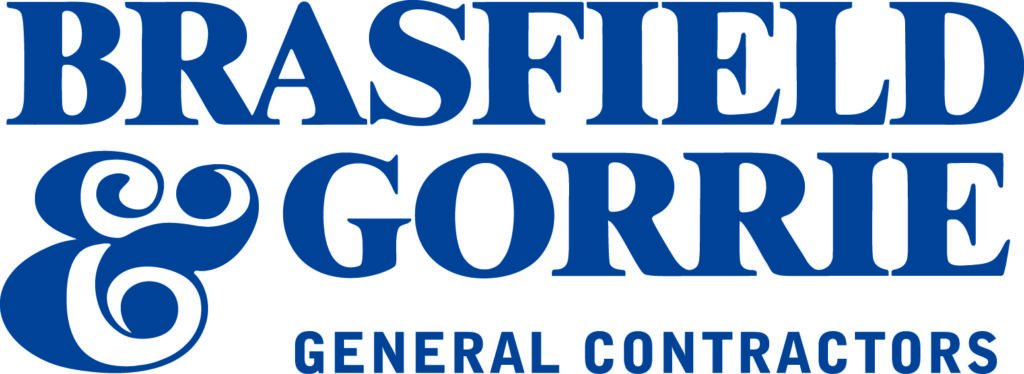
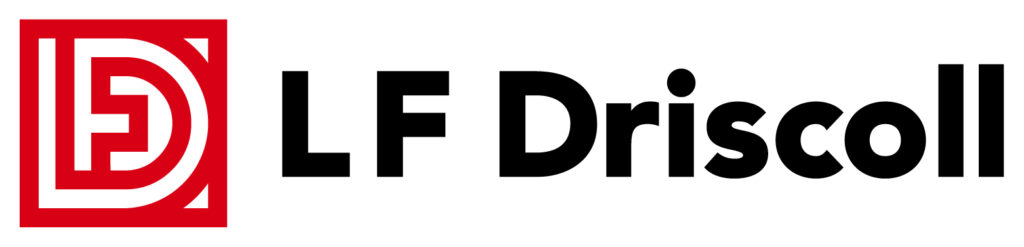
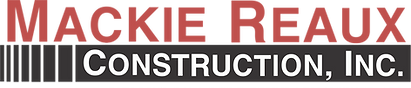
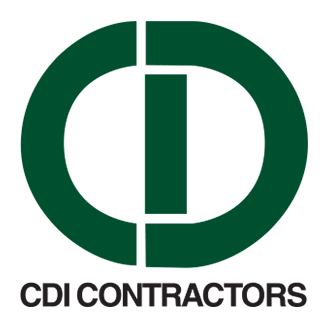


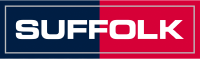

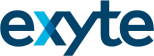
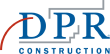
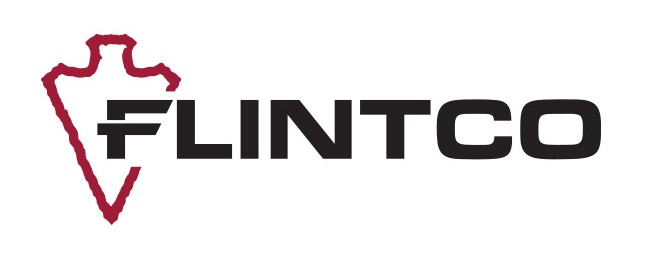
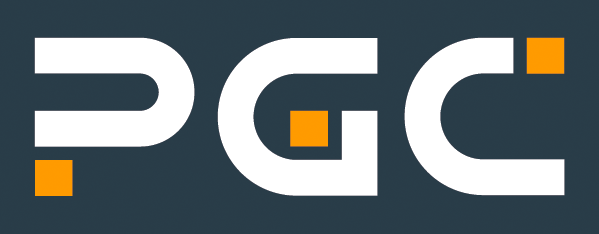
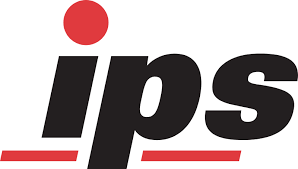
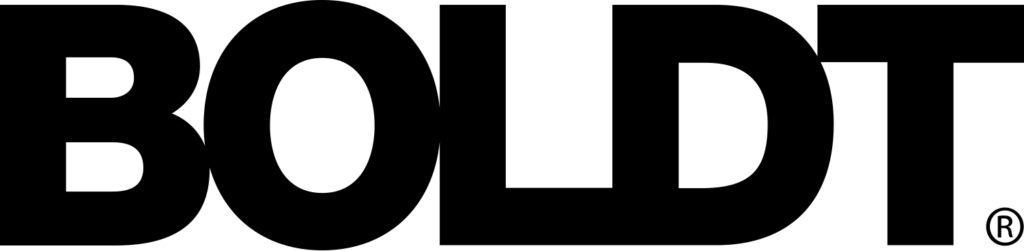
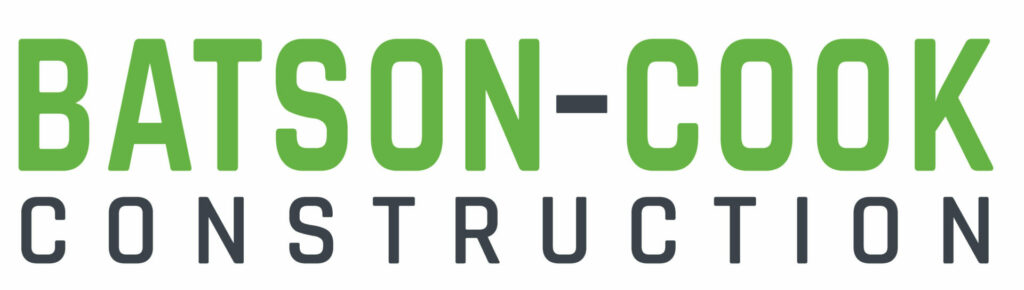
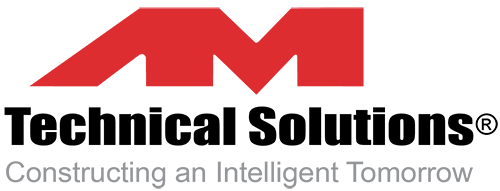
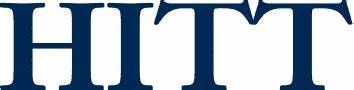
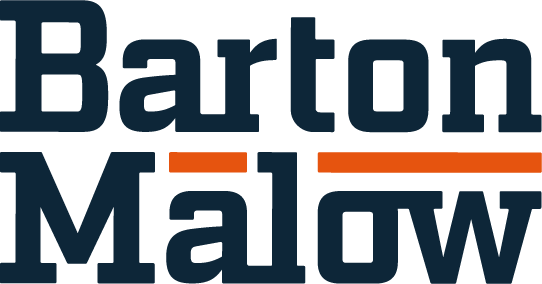

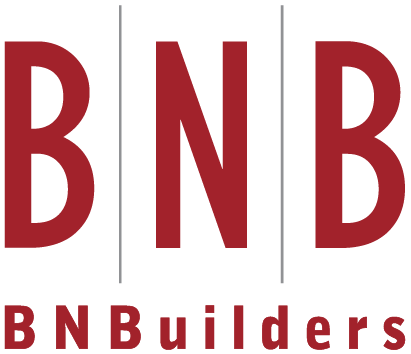
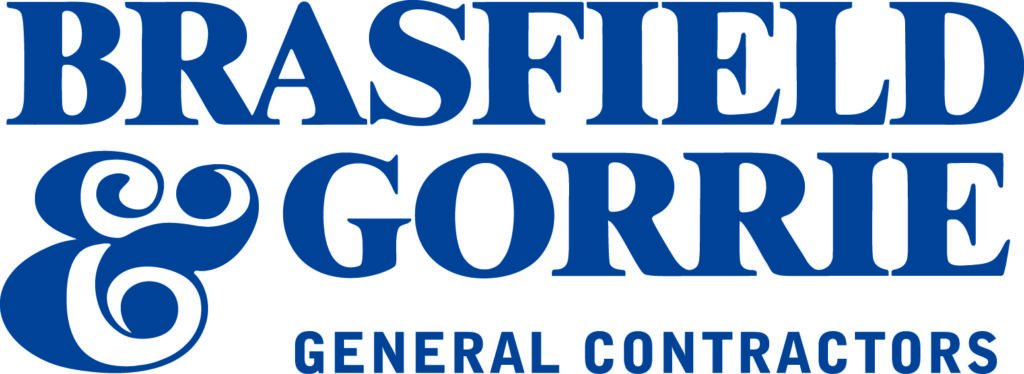
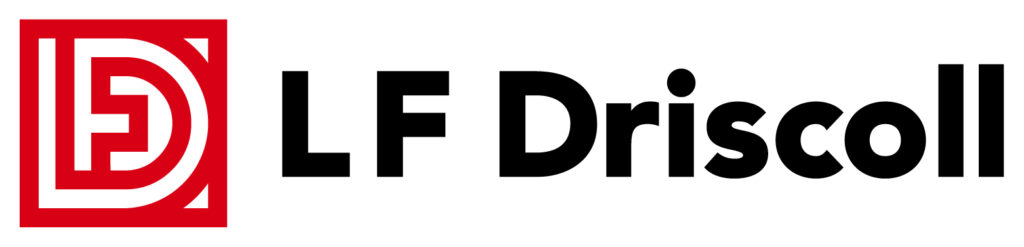
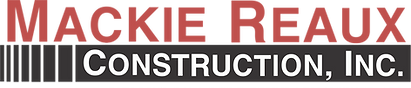
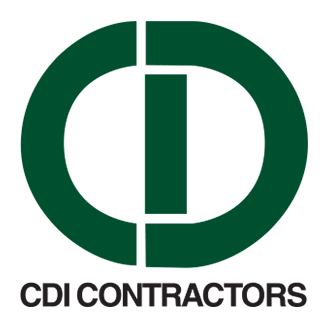


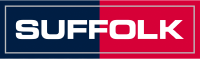

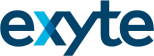
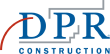
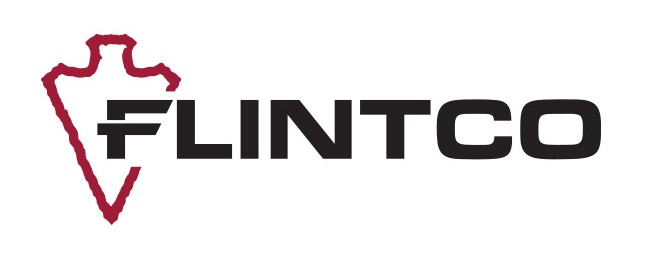
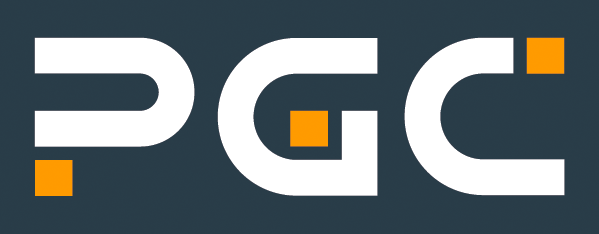
The big benefit here goes back to accountability and buy-in. The visual aspect of Touchplan has been very helpful in keeping our trade partners accountable, more so than when we were implementing Lean methodology with a manual approach. Touchplan brings a new level of accountability to the project.
Construction Executive, Caddell Construction
Master Scheduling
- In the Master Scheduling phase, teams will focus on building a Master Schedule that defines the major project milestones and goals for the construction project stage. Teams will conduct milestone planning by setting incremental goals that fit within the Master Schedule.
- Once the Master Schedule is set up, there are detailed best practices to follow related to a workflow for managing your Master Schedule and work plans in Touchplan.
- With Touchplan, teams can track progress against milestones, contribute to efficient work plans, and proactively address issues. Touchplan links Master Schedules from P6, Oracle Primavera Cloud, or Microsoft Project (coming soon) with jobsite activity to track and measure success.
Phase Scheduling
- At the Phase Planning level, the team takes the high-level tasks from the Master Schedule and begins to determine how the work should be executed by focusing on a specific phase and conducting a Pull Plan. The Pull Plan is the vehicle for the team to show their amazing ingenuity of how they are going to do it.
- Pull Planning is a collaborative process where trade partners work together to determine the best workflow for the job. By involving all stakeholders, the team focuses on key handoffs and workflow, fostering essential collaboration and communication to meet key dates. This process encourages open dialogue, early identification of challenges, and immediate solution development. Ultimately, the team learns to achieve deadlines while promoting safety, quality, and reliability in the schedule.
- With Touchplan, teams benefit from detailed visualization by breaking down specific project phases into manageable tasks, offering a clear view of the workflow. Touchplan facilitates collaborative Pull Planning sessions by enabling all stakeholders to contribute to the planning process and discuss the best sequence for work.
Look Ahead Planning
- The Look Ahead Planning phase is the step of LPS focused on “Can.” This is where the project team will first activate the sequence of work into a six-week look ahead schedule and start discussing what trade partners “can” do with the upcoming work, based on existing constraints.
- Identifying constraints as early as possible is key – this gives the project team and the trade partners time to clear these constraints, ensuring that they won’t hold up future work, and therefore make future work “ready” for other trade partners to start working. This significantly helps prevent any hiccups or holdups onsite and in the plan. The team will work together to figure out how to identify and remove constraints, record the information in a constraint log, and add any necessary tasks to the upcoming weeks.
- Touchplan supports the Make-Ready Planning phase by enabling teams to visualize and manage upcoming work based on current constraints. Its patented Active Line facilitates the transition from long-range planning to a detailed look-ahead schedule, while also managing accountability and identifying why tasks are not completed as promised. By recording constraints early in a constraint log, teams can proactively address issues, ensuring that future work is prepared and ready for execution, and allowing for quick, flexible re-planning.
Weekly Work Planning
- Weekly Work Plan Meetings, or Weekly Meetings, represent the “Will phase” in the Last Planner System. These meetings support collaborative and commitment-based planning, helping to develop a reliable workflow by ensuring all team members align their efforts and commitments. They provide each trade partner with the opportunity to commit to what they “will” do in the next seven days. The Weekly Meeting is a designated time for the project team and trade partners to discuss what happened since the last meeting, to learn from the past and to collaborate on the upcoming week’s work.
- With Touchplan and a structured process, the team can go beyond just talking about issues and get into solving them, always keeping the milestone end-goal in mind. This meeting allows trade partners and the project team to hold each other accountable, ensuring that plans for the upcoming week are confirmed and aligned.
- Flow can also be enhanced through the Daily Huddle, where the team reviews the previous day’s completed activities and discusses the current day’s tasks. This “Did” phase helps maintain safety, coordination, and adherence to plans, while fostering team culture and habits. With Touchplan Mobile, teams can update task statuses and access reports from anywhere, providing real-time insights and enhancing flexibility, responsiveness, and collaboration in the field.
- Teams rely on the Basic Variance Report and Percent Plan Complete (PPC) metrics to ensure focus during the weekly meeting. The variance report highlights pinned tasks that didn’t go according to plan within the selected timeframe, whether marked late, early, or still in progress without a status update. By comparing these tasks to the PPC, teams can assess how well they are adhering to the schedule and identify areas for improvement, ensuring accountability and driving continuous progress.
Learning
- Lean is designed as a feedback loop that helps teams continuously improve. The goal of Lean construction is not only to benefit from learning but also to become proactive problem solvers. Each team member strives to improve and overcome challenges.
- By reflecting on job site activities and areas for improvement, teams can immediately implement lessons learned. This leads to better planning and, more importantly, improved execution.
- Incorporating this learning step into every phase is crucial. Using Touchplan’s Analytics Dashboards and Reports helps teams drive discussions that enhance the planning process.
Make Lean Construction Easier
Touchplan’s simple, user-friendly interface has the look and feel of Sticky Notes, which reduces the learning curve and allows users to easily manage tasks and access projects anywhere, anytime. We make Lean Construction approachable with our ease of use, planning and daily recovery, collaboration, and comprehensive project data and analytics.
Ease of Use
- No knowledge of textbook terminology is required – teams can implement Touchplan during any stage of their Lean journey
- Includes onboarding/coaching on Lean best practices for every user
- Is the easiest way to capture stakeholder engagement
- Provides ongoing support to ensure Lean principles are reinforced
- Users receive customer support in 30 seconds or less
- Touchplan Mobile allows teams to make updates from their mobile device anywhere, anytime
Planning and Daily Recovery
- Supports multiple collaborative planning methods (LPS, Takt, IPD, etc.)
- Empowers teams to commit to an outcome, not to implementing the solution
- Pins represent real commitments, so plans are firmly rooted in reality
- Allows users to complete the full pull planning process without manually putting sticky notes on a wall
- Gives users the ability to convert their pull plan into the look ahead schedule
- Enables the entire team to complete all steps in the planning process beyond the master schedule, all within a single platform
- Teams can easily identify constraints to better manage roadblocks
Collaboration
- Focuses on the people actually doing the work, enabling everyone to contribute and highlighting the importance of teamwork for smooth operations
- Invites all team members into the planning environment by offering access to unlimited users
- Collaborative pull planning combined with weekly work planning enables users to continuously update plans, stay on schedule, and document detailed variance reasons when encountering roadblocks
- Teams can track who is doing what and how it’s being done through a clear member performance view, enhancing communication and promoting effective collaboration
- From trades to the Owner, gain buy-in and engagement from all stakeholders
Project Data and Analytics
- The digital process offers robust analytics that is often missed with manual planning
- Gain data-driven insights with constant updates on team performance, keep everyone automatically informed, and improve project efficiency
- Fosters optimal alignment, collaboration, and communication with owners and their vision
- Ensures that lessons learned from a project improve future processes, improving overall project certainty
Our History with Lean Construction
MOCA Systems, Inc. began an as outgrowth of MIT research in construction simulation and planning in 1999. Over a decade later, we began to see teams using sticky notes on the walls of construction site trailers to keep track of plans. Frustrated by sticky notes falling off walls, constantly rearranging them, taking photos to track progress, and frequently restocking supplies, we realized there had to be a better way to plan construction projects. In 2013, that better way became a reality with Touchplan.
With the creation of Touchplan, we balance an established dedication to LPS principles with a firm-wide commitment to making Lean approachable for all stakeholders and team members during any stage of their Lean journey. Giving team members the ability to collaborate, be more efficient, get straightforward analytics, and keep track of tasks in real-time makes projects more efficient and delivers better results.
Today, Touchplan has evolved into the most widely-used Lean construction planning platform and provides easier access to plans with its mobile interface, patented Active Line technology, analytics dashboards, API, Master Schedule synchronization, and so much more.
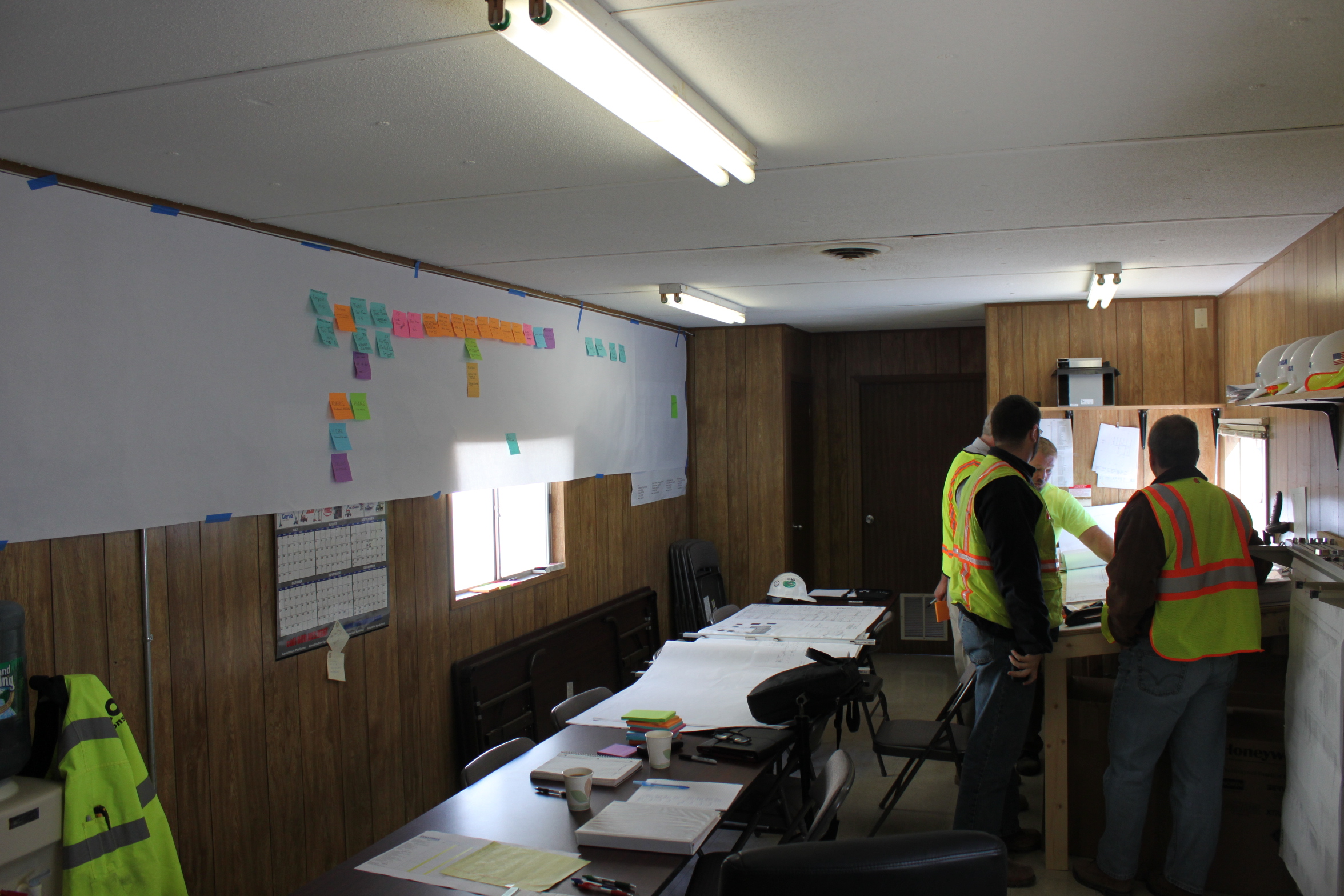
Lean Construction Resources
Ready to get in touch?
Whether you have a question about features, demos, pricing or anything else, we’re here to help.
By submitting this form, I agree to the Terms of Use and the use of my personal information as described in the Privacy Policy